Introduction
Silicone rubber compression molding is an invaluable manufacturing process in multiple industries. This technique uses compression of silicone rubber to produce high-quality rubber parts and seals. Understanding its associated costs is vital for businesses seeking to optimize production while realizing cost savings.
Accurately calculating the costs associated with silicone rubber compression molding requires taking into account a range of variables, including material costs, mold design and production expenses, labor, equipment costs, energy consumption rates, scrap and waste, quality inspection costs as well as scrap. By studying all these elements together businesses can gain insights into overall compression molding expenses as well as take steps to lower them while maintaining product quality.
As we explore key factors influencing silicone rubber compression molding cost calculations and provide practical guidance, we will also offer insight into effective cost calculation. By becoming experts on cost calculations, businesses can make informed decisions, streamline operations, and achieve cost savings without compromising product quality.
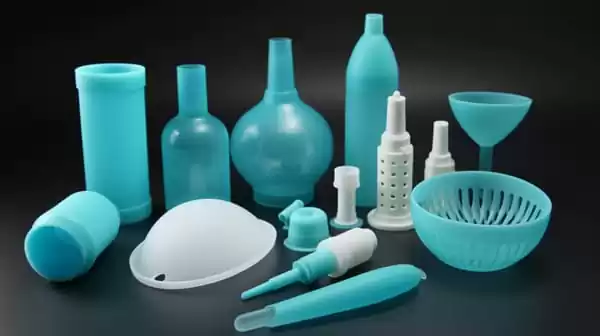
II. Factors Affecting Cost in Silicone Rubber Compression Molding
A. Material Cost Effective
The cost of materials is a crucial factor to consider when calculating the overall cost of silicone rubber compression molding. It includes:
- Different silicone rubber compounds and their costs: Silicone rubber is available in various formulations and grades, each with its own price point. Factors such as the desired properties of the final product and industry requirements influence the selection of the appropriate silicone rubber compound.
- Calculating the amount of rubber required for the mold: Accurately determining the quantity of silicone rubber needed for the mold is essential for cost estimation. Factors to consider include the size and complexity of the part, material thickness, and any additional waste or excess material.
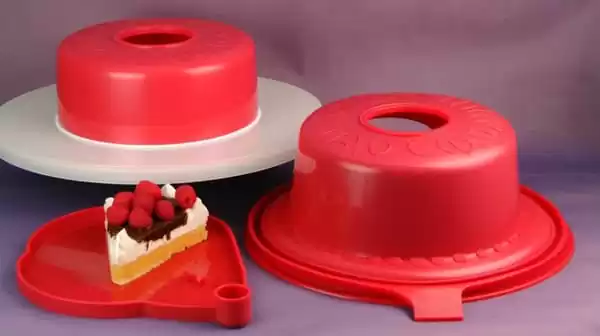
B. Mold Design and Production Cost
The design and production of the compression mold significantly impact the overall cost. Consider the following factors:
- Complexity of mold design and number of cavities: The complexity of the mold design and the number of cavities required for each mold affect the cost. Intricate designs or molds with multiple cavities may require additional machining, resulting in higher production costs.
- Impact of cycle time on cost: The cycle time, which includes the molding, cooling, and curing stages, affects production capacity and cost. Minimizing cycle time through efficient process optimization can lead to cost savings.
- Compression mold tooling considerations: The cost of tooling, including the manufacturing and maintenance of compression molds, is an important factor to consider. Proper maintenance and regular inspections help prolong the mold’s lifespan and reduce long-term expenses.
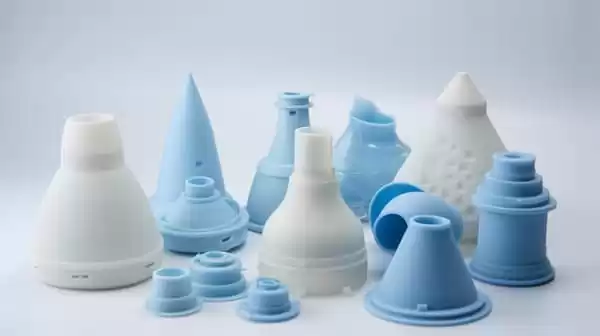
C. Production Cost Effective
Several factors contribute to the overall production cost in silicone rubber compression molding. These include:
1.Labor costs associated with machine operation, mold preparation, and quality inspections: Skilled labor is required to operate the molding machine, prepare the mold, and perform quality inspections throughout final stage of the production process. Consider the labor hours involved and the associated costs.
2.Equipment and energy expenses:
The cost of equipment, including molding machines and auxiliary devices, should be considered. Additionally, energy consumption during the molding process contributes to the production cost.
3.Scrap and waste management:
Efficient material usage and waste management play a role in cost optimization. Minimizing scrap and waste by optimizing the mold design and production process can lead to significant cost savings.
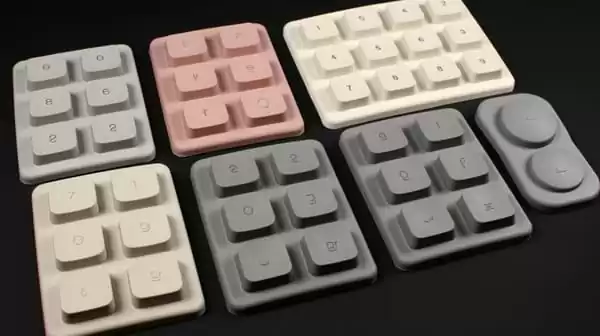
4.Cost of quality inspection and testing:
Ensuring the final product meets the required quality standards involves inspection and testing procedures. Incorporate the cost of these quality control measures into the overall production cost.
By taking these factors into account, businesses can accurately calculate the cost of silicone rubber compression molding and identify opportunities for cost optimization throughout the process.
III. How to Calculate the Cost of Silicone Rubber Compression Molding
A. Step-by-step process for cost calculation
1.Determining material costs:
To calculate the material cost for silicone rubber compression molding, follow these steps:
a. Identify the specific silicone rubber compound required for the application.
b. Research the cost per unit weight for the chosen silicone rubber compound.
c. Calculate the amount of silicone rubber required for the mold based on the desired shape and size of the final product.
d. Consider any additional waste or excess material that may need to be accounted for.
e. Multiply the quantity of silicone rubber required by the cost per unit weight to determine the material cost.
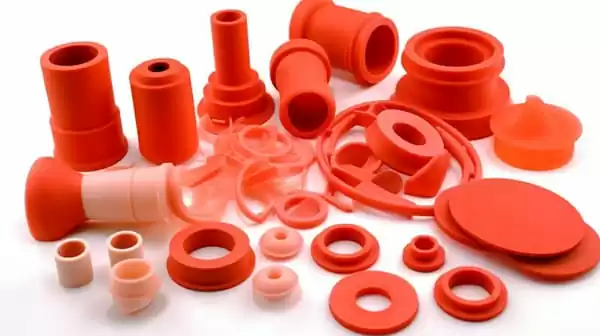
2.Assessing mold design and production expenses:
To calculate the mold design and production expenses, consider the following factors:
a. Evaluate the complexity of the mold design single cavity mold and the number of cavities required.
b. Determine the impact of cycle time on production costs.
c. Account for the cost of compression mold tooling, including the manufacturing and maintenance of the molds.
d. Consider any additional expenses associated with mold design modifications or customization.
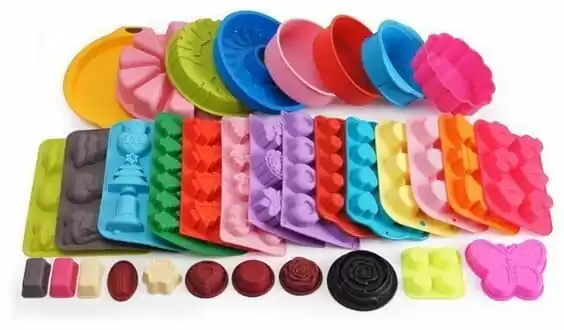
3.Evaluating overall production costs:
To calculate the overall production costs, consider the following:
- a. Assess labor costs associated with machine operation, mold preparation, and quality inspections. b. Include the expenses related to equipment, such as molding machines and auxiliary devices. c. Account for energy consumption during the production process. d. Consider scrap and waste management costs, including the handling and disposal of excess material or waste products. e. Incorporate the cost of quality inspection and testing procedures to ensure compliance with required standards.
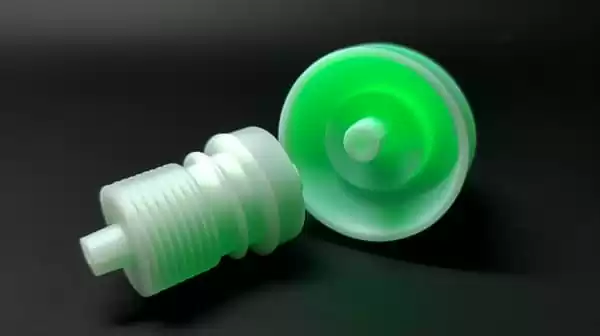
By meticulously calculating these cost components and adding them together, businesses can determine the overall cost of silicone rubber compression and injection molding. This comprehensive understanding of the cost structure allows for better decision-making, cost optimization, and improved profitability.
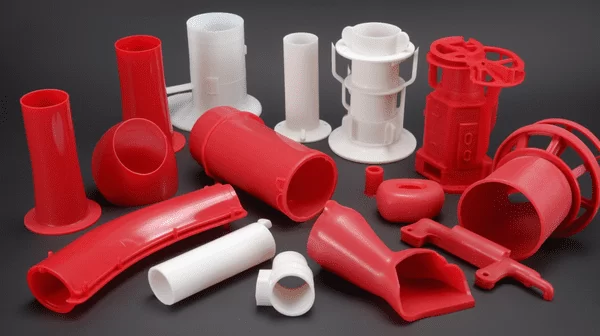
V. Tips for Cost Optimization
A. Strategies to minimize material waste
- Accurate material estimation: Properly calculate the required amount of silicone rubber for each mold to minimize material waste. Consider factors such as part dimensions, thickness, and any additional material allowances.
- Recycling and reusing excess material: Implement a system to collect and reuse excess silicone rubber from the molding process. Recycled material can be used for less critical or non-visible parts, reducing material costs.
- Optimized mold design: Design molds that minimize material usage by incorporating features such as efficient gating systems and parting lines. This reduces scrap and waste during the production process.
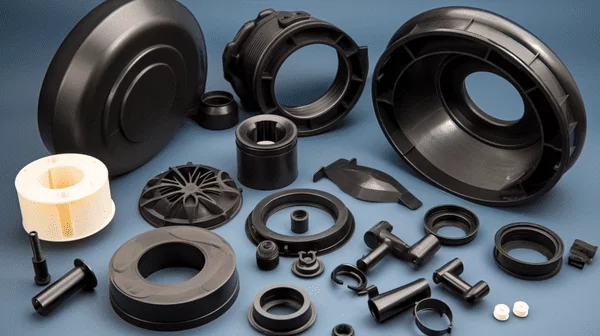
B. Enhancing mold design and production efficiency
- Design for manufacturability: Ensure that the mold design is optimized for efficient production. Consider factors such as part complexity, mold maintenance requirements, and ease of demolding to enhance production efficiency and reduce costs.
- Multi-cavity molds: Utilize multi-cavity molds to increase production output without significantly increasing costs. This approach reduces the number of mold setups required, resulting in higher productivity and lower overall production costs.
- Automation and technology integration: Explore automation options, such as robotic part handling or automated mold loading, to streamline the production process and reduce labor costs. Integrate advanced technologies like simulation software for mold design optimization and process analysis.
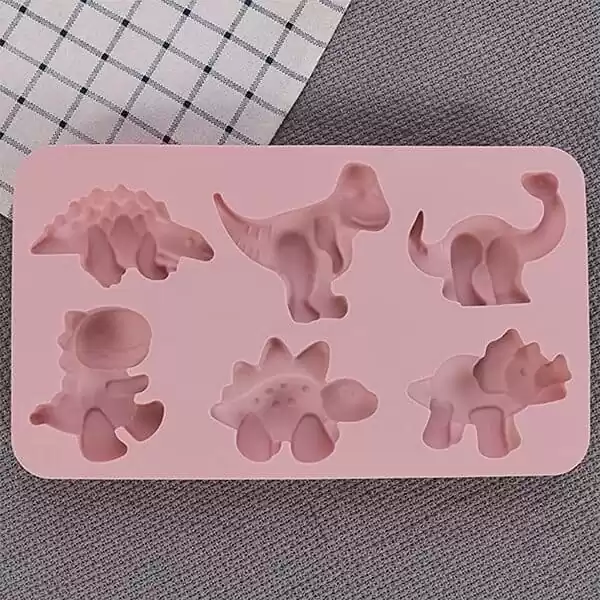
C. Reducing cycle time for increased productivity
- Process optimization: Analyze the compression molding process parameters to identify opportunities for reducing cycle time. Optimize variables such as temperature, pressure, and curing time to improve productivity and shorten the overall production cycle.
- Mold temperature management: Implement efficient mold cooling systems to accelerate the cooling and curing stages. Proper mold temperature control reduces cycle time and increases production efficiency.
- Advanced molding techniques: Consider advanced molding techniques such as rapid heating and cooling methods or the use of preheated molds to reduce cycle time. These techniques can result in significant time savings and increased productivity.
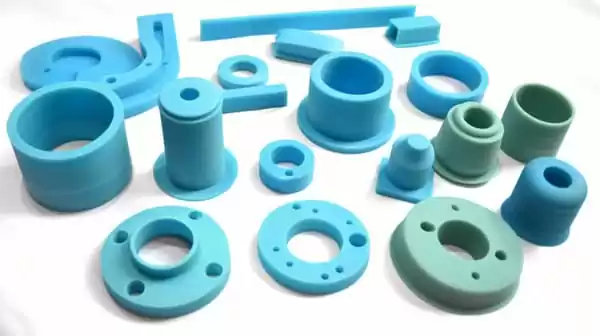
By implementing these cost optimization strategies, businesses can reduce material waste, enhance injection mold part design and production efficiency, and shorten cycle times. These efforts contribute to improved productivity, lower production costs, and increased competitiveness in the silicone rubber compression molding industry.
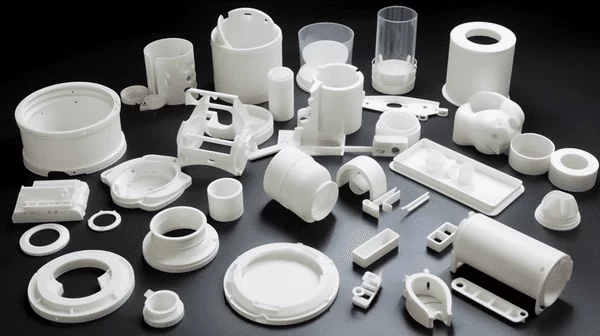
Conclusion
In conclusion, understanding the cost calculation in silicone rubber compression molding is vital for businesses to optimize their operations and achieve cost savings. By considering key factors and utilizing appropriate formulas, businesses can accurately determine the overall cost of the process. Let’s recap the essential elements:
- Material cost: Calculate the cost of silicone rubber compounds based on their unit weight and determine the quantity of rubber required for the mold.
- Mold design and production cost: Consider the complexity of the mold design, the number of cavities, the impact of cycle time on cost, and the expenses related to compression mold tooling.
- Production cost: Assess labor costs associated with machine operation, mold preparation, and quality inspections. Include equipment and energy expenses, manage scrap and waste efficiently, and consider the cost of quality inspection and testing.
Understanding these cost components enables businesses to make informed decisions. It helps identify areas for cost optimization, streamline operations, and achieve cost savings without compromising product quality. By minimizing material waste, enhancing mold design and production efficiency, and reducing cycle time, businesses can enhance productivity and reduce overall production costs.
In the competitive landscape of silicone rubber compression molding, cost optimization plays a crucial role in profitability and market competitiveness. Businesses that prioritize understanding and effectively managing costs have the opportunity to achieve long-term success. By applying the tips and strategies discussed, businesses can optimize their operations, increase cost-effectiveness, and deliver high-quality silicone rubber compression molded products.
In summary, a comprehensive understanding of cost calculation s in silicone rubber compression molding empowers businesses to make informed decisions, identify cost-saving opportunities, and achieve sustainable growth in the industry.