Silicone is a material that seems to be everywhere these days, from life-saving medical devices in doctor’s offices to bakeware hiding in kitchen cabinets. It is elastic, resistant to extreme temperatures, and has excellent electrical insulating properties.
Silicone rubber is a versatile material used in many different industries. It has unique properties that make it stand out from other types of rubber, but that also means it can be more expensive. Why does silicone cost more? What are the benefits of using it compared to cheaper alternatives? We take an in-depth look at the factors driving the price of this premium product and its benefits, as well as we break down the factors that impact the cost of silicone and the benefits that justify the investment.
Silicones cost more than other polymers, likely because silicone’s complexity, performance advantages, and specialized manufacturing play a crucial role in its high pricing. In this blog post, we’ll dive into each of these elements, providing illuminating insights into the hidden costs of this remarkable polymer.
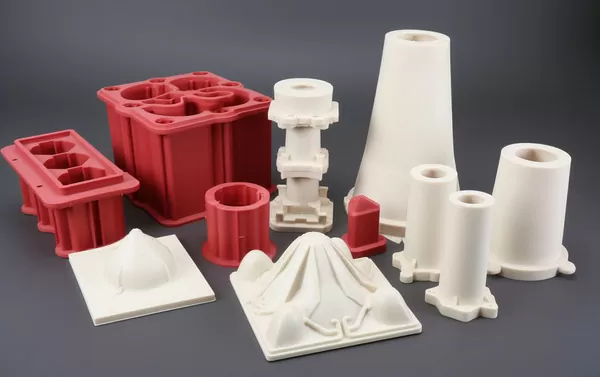
Rubber Basics
Before we extol the virtues of silicone, it’s important to understand its place among other types of rubber. The term “rubber” refers to an elastomer, a polymer that stretches and then springs back to its original shape. Natural rubber, made from trees, was the first such material used by humans, but as technology advanced, many synthetic materials were created, such as neoprene and polyurethane.
Each rubber has its own unique qualities that make it ideal for certain applications:
Natural Rubber (NR): Very elastic and tough. That’s why we use it to make products like tires, elastic bands, and protective gloves.
Styrene Butadiene Rubber (SBR): A man-made synthetic rubber that does many different jobs well. Its abrasion resistance is better than natural rubber. This makes SBR ideal for building tires that will last for a long time.
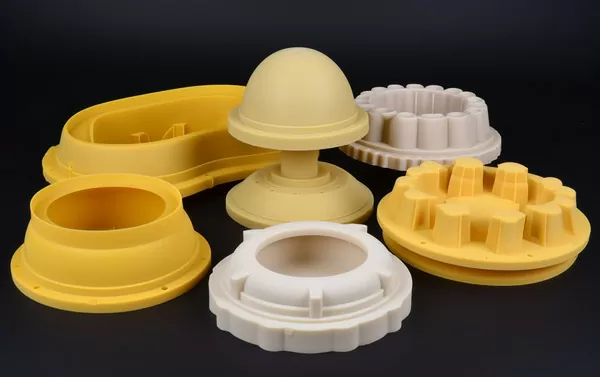
Neoprene (CR): CR is a synthetic rubber with very balanced properties. Its excellent oil resistance and strong adaptability to climate and temperature changes make it very suitable for making seals, gaskets or hoses. wait.
Polyurethane Rubber (PU): PU has high elongation properties, so it can be stretched a lot. So ideal for making suspension bushings or rollers.
Each type has its unique advantages, but also its limitations. This is where the exceptional properties of silicone come into play.
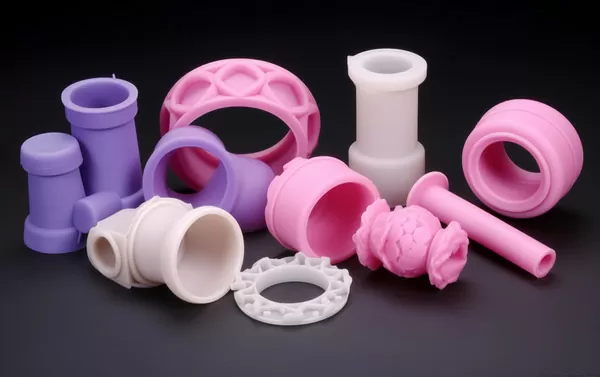
Silicone: A Structure of Stability
Silicone rubber material is a synthetic elastomer made primarily from silicone. Silicones are composed of silicon, carbon, hydrogen and oxygen. Because their chemical structure is different from natural rubber or neoprene (two other types of elastomers), silicones also have different properties.
For example: Even withstand extreme temperatures, they will not decompose like organic rubber. Silicone is naturally resistant to ultraviolet (UV) and ozone, which means it can not only withstand heat but also be used outdoors for extended periods of time without significant harmful effects. Manufacturing these tough, chemical-resistant materials requires expertise and is expensive.
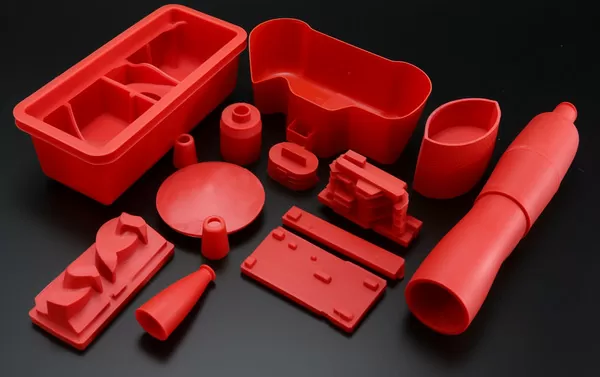
Silicone is not a single material but a polymer, and this family of polymers gives it an unusual combination of properties that are not commonly found in other rubbers. Silicones have many useful properties:
Temperature Resistance: Silicones can withstand high temperatures without significant decomposition. They can withstand temperatures from -100°C to 250°C, sometimes even higher if specially treated. That’s why silicone rubber is used not only in oven mitts, but also in electronics on spacecraft and satellites.
Chemical Resistance: Silicones are resistant to a wide range of chemicals, making them ideal for silicone sealants that come in contact with oils, salts, acids, and alkalis.
Biocompatibility: If you are using them for medical purposes, they will not react with your body tissue and are also safe to use in food.
Electrical Insulation Properties: Silicone is a good electrical insulator, which means it protects against leakage of electricity very well.
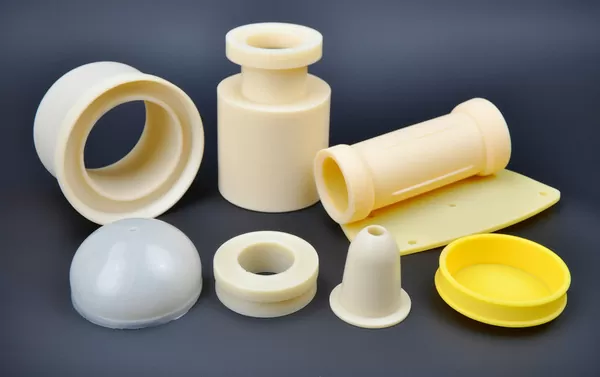
Weather Resistance: Finally don’t forget that these substances are weatherproof; able to withstand the attack of ultraviolet rays from the sun and ozone gases: this combination can quickly break down most materials left outside.
It is this rare combination of thermal stability, chemical inertness and biocompatibility that allows silicones to stand out as high-performance polymers.
The Raw Material Dilemma
Silicone rubber is composed of silicone, a polymer containing silicon, carbon, hydrogen and oxygen. Obtaining pure silicones can be more expensive than carbon-based silicones because it requires a lot of refining and processing of these special substances!
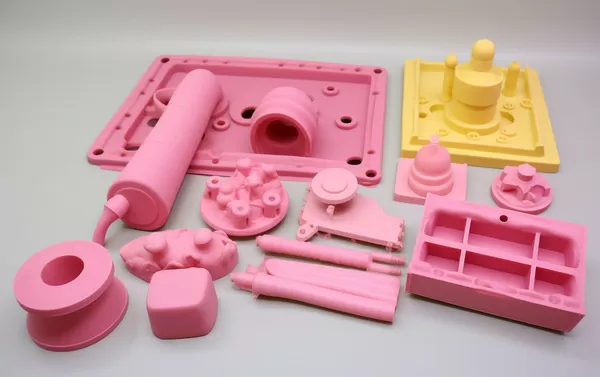
In fact, the refining of the silicon extracted from silica itself is an energy-intensive process that significantly increases the production costs of the raw material.
The Relevance of Purity
The purity of the raw materials used to make silicone has a large impact on its cost. When silicones are very pure, they tend to have better physical and chemical properties than less pure silicones. This makes high-purity silicones ideal for medical devices, aerospace equipment, and electronics with best-in-class performance, among others. Ensuring that the silicone remains ultra-pure throughout the manufacturing process is more expensive, and these additional costs ultimately drive up the price.
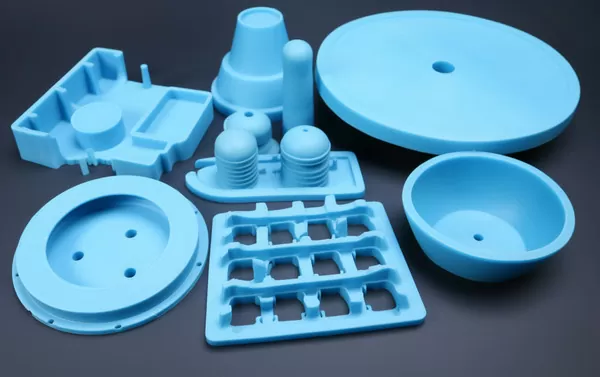
Manufacturing Complexity
The production process of silicone rubber is usually more complex than that of regular rubber. This is because there are extra steps involved, such as high-temperature curing and cross-linking, that are necessary if you want your silicone to have specific qualities, such as being able to withstand very hot or very cold temperatures better than most substances or withstand repeated stress.
These steps ensure that the product maintains stable performance or appearance when repeatedly exposed to sunlight (UV) or even normal atmospheric levels of oxygenated air (ozone) for extended periods of time. These different properties combined really make them very useful.
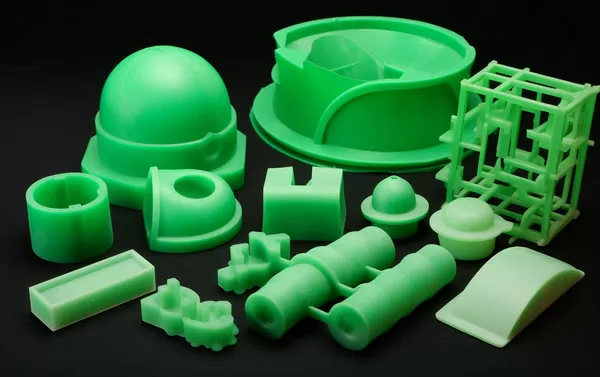
Quality Over Quantity
When it comes to silicone rubber production, quality is often more important than quantity. Manufacturers often focus on accuracy throughout the production process, an approach that helps them meet strict industry specifications and individual customer needs with enough precision to justify the higher costs associated with more complex manufacturing procedures.
Durability and Longevity
Silicone rubber’s exceptional durability sets it apart from other materials and justifies its higher price. In fact, silicone rubber products usually last much longer than similar products. In the long run, they will become cheaper and more cost-effective.
They need to be replaced less frequently than similar products made from different substances, and maintenance costs are generally lower (although the initial cost may be relatively high).
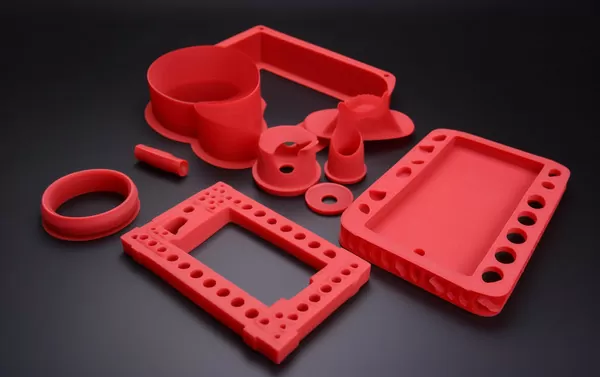
Environmental and Chemical Resistance
Another advantage of silicone material is its natural resistance to chemicals and environmental conditions. This means that products made from silicone can maintain their strength, look and function well for a longer period of time, whether used in harsh environments or exposed to the elements for long periods of time, helping people pay more up front. The cost, as it is long-lasting, can also further justify the investment in a role where resiliency is critical.
Manufacturing Mastery
The processing of silicone rubber is different from traditional rubber and requires special technologies such as compression molding, transfer molding, and liquid injection molding:
Compression Molding: An inexpensive method of producing consistent low- or medium-volume silicone products.
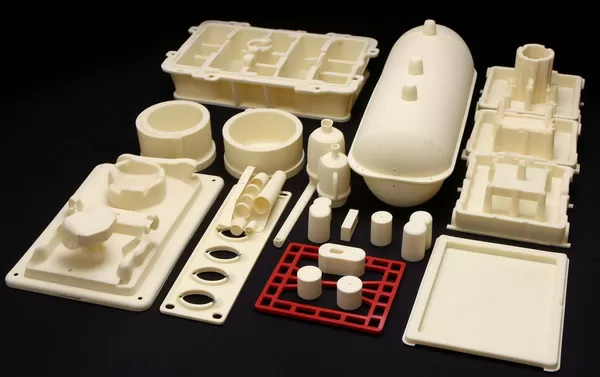
Transfer Molding: Transfer molding works well when you need a large number of accurately formed items without wasting material, making it less expensive than other methods for complex parts.
Liquid Injection Molding: The upfront cost of liquid injection molding may be higher, but if your product needs to have a high level of precision with both heat resistance and precise shape, this technology offers tremendous value.
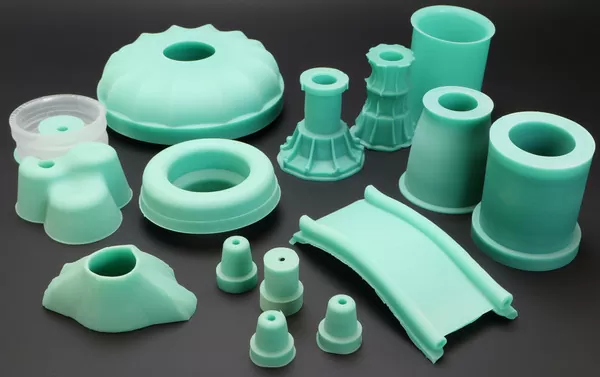
Because silicones require longer curing times and higher curing temperatures than traditional rubber materials, the manufacturing process needs to be carefully controlled. Additionally, due to its specialized nature, the cost of manufacturing equipment rises accordingly, meaning increased capital investment is passed on to customers.
Compliance and Certification
The use of silicone rubber is common where strict rules must be followed. For example, in the automotive industry, medical and food sectors, silicone products need to meet FDA guidelines as well as those of other regulatory agencies around the world. Complying with these protocols means increasing costs to a certain extent, however, it does ensure that customers’ products are safe and comply with industry standards.
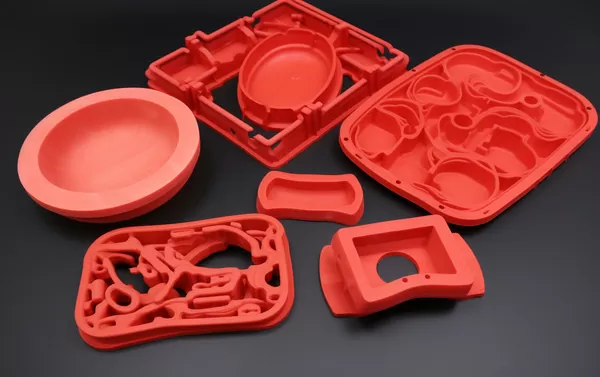
Specialized Certifications
In addition, certain silicone products must meet industry-specific certification requirements. For example, medical implants need to be biocompatible and aerospace materials should be flame retardant.
While obtaining these certifications does require additional testing and recording procedures, which results in increased costs, these steps are necessary to ensure fitness for the intended use, as conventional compliance measures alone cannot provide certainty.
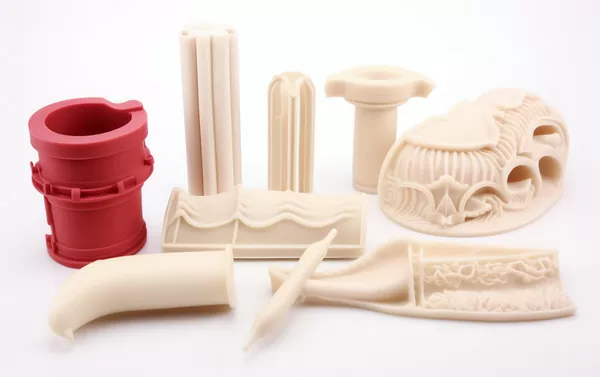
Innovation and Research
Because silicone rubber is such a versatile substance, it tends to attract significant R&D investment and funding. Scientists continue to develop new silicone combinations that perform better than before, and they do this by using the latest technologies in materials science and manufacturing processes.
All this continuous improvement means one thing for users: their products will always be at the leading edge in areas such as electronics or healthcare, although costs may rise due to two factors: the continued need for R&D spending and meeting domestic/ Internationally mandated regulations, which sometimes drive up prices significantly.
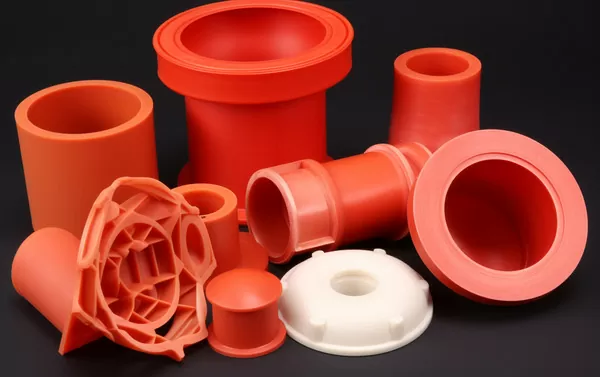
Tailored Solutions
The silicone rubber industry is customer-driven, which means many companies are willing to customize their products to meet the needs of specific projects. While this may increase costs compared to off-the-shelf products from competing companies, being able to deliver exactly what customers want provides unparalleled value in the market.
Sustainability and Cost Considerations
In the search for sustainability, new ways of making rubber have been found. For example, bio-based elastomers: made from renewable plants and other natural substances. Using this new type of material instead of old-fashioned types may help save the planet. But there are also disadvantages, such as the performance they present cannot yet match that of silicones in the key areas of high temperature and chemical resistance.
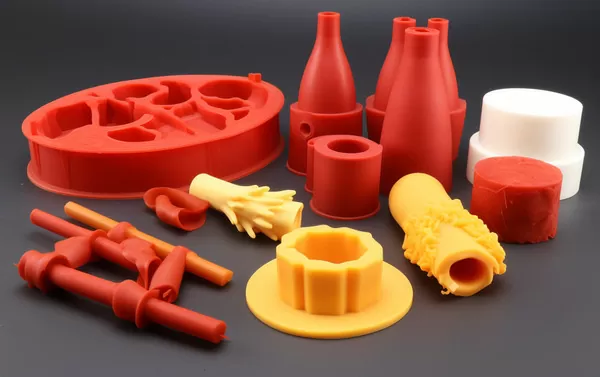
Conclusion
Silicone rubber costs less than similar rubbers for a very good reason: First, silicones have physical and chemical properties that are second to none. In addition, manufacturers are now willing to take extensive measures to ensure that their products meet strict standards, so the upfront investment cost of silicone is relatively high. Whether your application requires materials that can withstand harsh conditions over time, or must meet requirements imposed by industry regulators, there is no better choice than high-quality silicone.
The cost of silicone rubber includes more than just manufacturing costs. It also includes what is needed to develop and produce such materials: deep chemical knowledge and systems for large-scale development and production. In addition to the stability, versatility, and other benefits that make it worth the investment, there’s a lot of behind-the-scenes work that makes it very expensive.
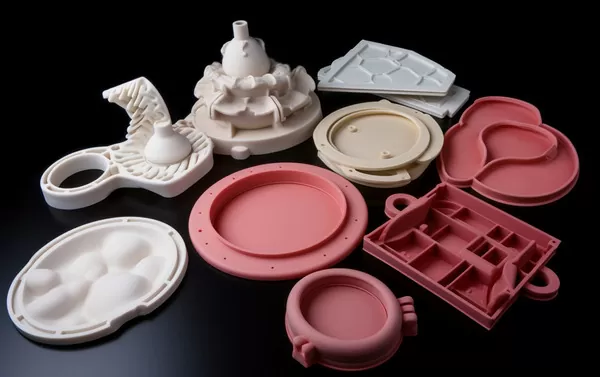
Although silicone is more expensive, the unique properties of silicone still inspire new ideas in many fields. The material can do things that other rubbers cannot. As our demand for tougher materials that can work in harsh environments rises, so does our reliance on silicones.
As we delve deeper into the world of silicones, its value becomes clear. Whether it’s silicone seals necessary for jet engines or silicone rubber items used in everyday life, this material offers better performance than many alternatives. Despite its higher price, its irreplaceability makes it highly desirable.